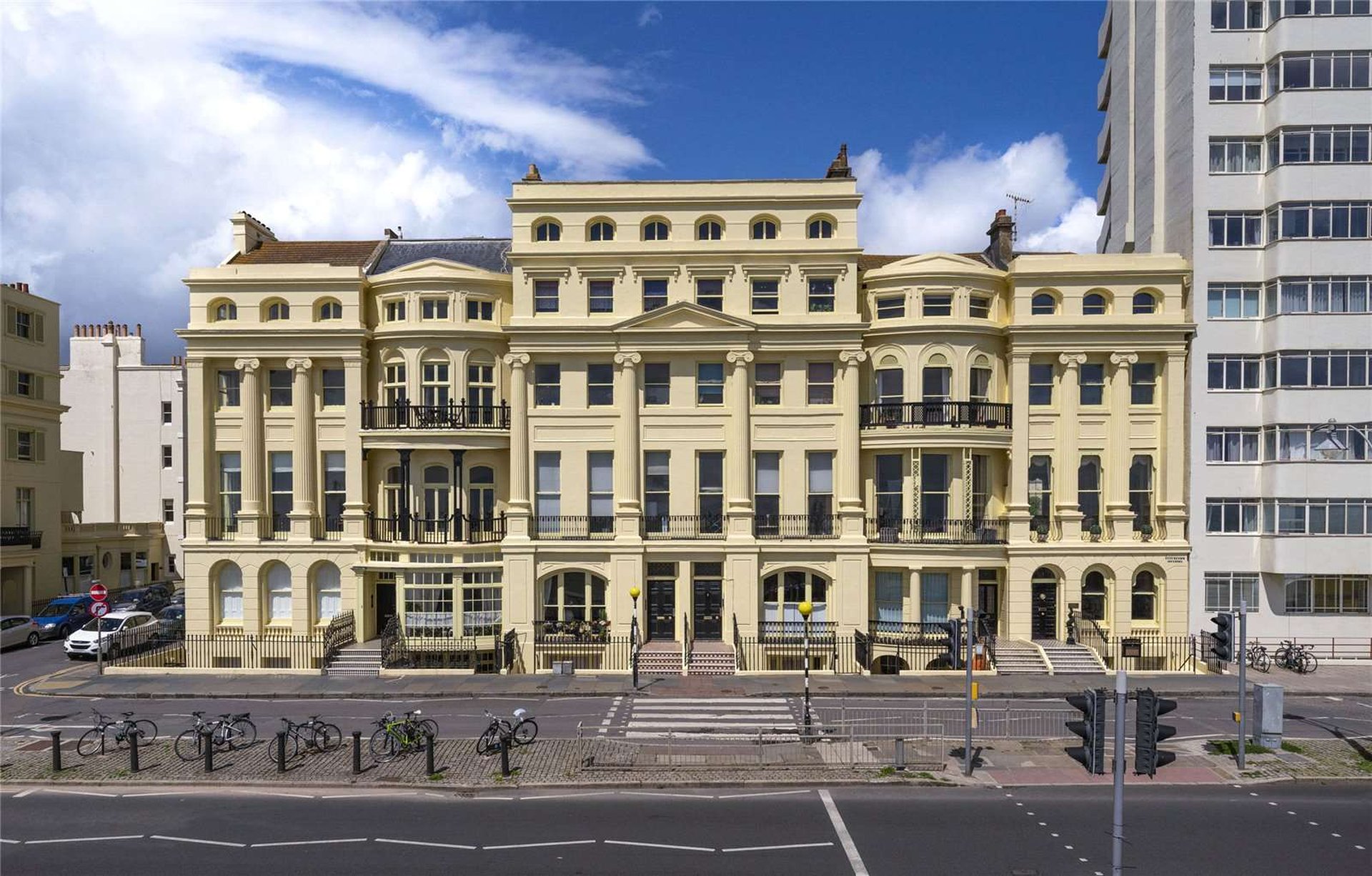
Traditional & Modern Rendering in Brighton & Hove — The Safe-Bricks Service Guide
Table of Contents
Introduction
Rendering & Brighton’s Coastal Climate
Traditional Renders
Modern Render Systems
Breathability, Moisture & Thermal Upgrades
Planning Permission & Listed-Building Rules
Substrate Considerations: Brick, Block, Bungaroosh & EWI
Colour, Texture & Finish Options
The Rendering Process: Step-by-Step
Cost & Budget Planning
Choosing a Specialist Contractor
Maintenance & After-Care
Frequently Asked Questions
Further Reading & Spin-Off Articles
Next Steps
1 Introduction
Rendering is the protective and decorative skin that shields Brighton & Hove’s homes from relentless salt-laden winds, driving rain and intense UV glare. Whether you own a Regency stucco townhouse, a Victorian bungaroosh terrace or a contemporary eco-build, the right render system preserves structural fabric, improves thermal performance and elevates kerb appeal.
This comprehensive guide walks you through every stage of the rendering journey—from choosing lime putty for heritage façades to specifying silicone top-coats on new extensions—and links out to in-depth articles that address each specialist niche in far greater detail.
2 Rendering & Brighton’s Coastal Climate
Sea spray accelerates erosion, while fluctuating humidity pushes moisture deep into porous masonry. Standard sand-cement mixes often crack and trap damp; advanced polymer coatings can cope better but may suffocate older walls. Selecting a render that balances weather-proofing with breathability is critical.
Further reading: Choosing the Right Render for Coastal Homes in Sussex
3 Traditional Renders
3.1 Lime Putty Render
Composition: Non-hydraulic lime putty, sharp sand, natural fibres.
Benefits: Highly breathable, flexible, self-healing hairline cracks.
Ideal For: Bungaroosh, soft brick, listed façades.
Further reading: Lime Render vs. Cement Render — Pros & Cons
3.2 Hot-Lime & NHL (Natural Hydraulic Lime)
Faster set than air-lime, suitable for exposed elevations.
Suits damp basements or seafront gables that face prevailing winds.
3.3 Traditional Stucco (Regency & early-Victorian)
Multi-coat system ending with a smooth “setting coat” polished with tallow.
Requires skilled application to replicate ashlar block lines or rusticated bands.
4 Modern Render Systems
4.1 Sand-Cement Render
Budget-friendly but prone to cracking on old substrates. Increasingly replaced by flexible alternatives.
4.2 Monocouche (Through-Colour)
Single-coat, polymer-modified cementitious render.
Factory-pigmented, minimal post-paint maintenance.
Popular on new-builds and loft-conversion gables.
Further reading: Monocouche Colour Guide for Brighton Extensions
4.3 Silicone & Acrylic Thin-Coat
Applied over a base-coat with fibreglass mesh.
Highly water-shedding yet vapour-permeable.
Ideal for External Wall Insulation (EWI) retrofits.
4.4 Clay & Hemp-Lime Finishes
Eco-friendly, ultra-breathable, suited to internal feature walls and eco-homes.
5 Breathability, Moisture & Thermal Upgrades
Salt, wind-driven rain and internal condensation converge in coastal homes. Breathable renders allow vapour to escape; impermeable systems risk blistering and spalling.
External Wall Insulation (EWI) plus thin-coat silicone can cut heat loss by up to 40 %.
Internal Insulated Lime Plasters maintain breathability on listed interiors.
6 Planning Permission & Listed-Building Rules
Brighton & Hove hosts 34 conservation areas and over 3,400 listed structures. Changing render colour, texture or profile on a principal façade may need consent.
Listed Building Consent: Essential for lime-stucco stuccoes or rusticated Regency fronts.
Conservation Area Guidance: Colour palettes often restricted to pale stone hues.
Further reading: Rendering in Conservation Areas — Dos & Don’ts for Brighton Homeowners
7 Substrate Considerations: Brick, Block, Bungaroosh & EWI
SubstrateRisksRecommended RenderKey PrepBungarooshSalt & voidsLime putty / NHL 2Rake out cement pointing, install chestnut laths if unevenSoft Victorian BrickFrost spallingNHL 3.5 base + lime finishLow-pressure wash, lime slurry bonding coatModern BlockworkShrinkage cracksMonocouche or silicone thin-coatFibreglass mesh, stop-beads, expansion jointsEWI BoardsImpact & UVAcrylic or silicone thin-coatAlkali mesh embedded in base-coat
Further reading: Rendering Bungaroosh Walls — Specialist Techniques & Pitfalls
8 Colour, Texture & Finish Options
Smooth Float: Classic stucco sheen for Regency terraces.
Scraped Monocouche: Subtle grain, no paint required.
Roughcast / Pebble-Dash: Ultra-durable on exposed seafront cottages.
Ashlar Lines: Imitate stone blocks in lime stucco.
Coloured Silicone: Over 300 RAL shades, UV-stable.
9 The Rendering Process: Step-by-Step
Survey & Moisture Testing
Substrate Repair & Prep — Remove loose material, replace corroded fixings.
Primer or Slurry Coat — Ensures adhesion.
Base-Coat / Scratch-Coat — Incorporate fibreglass mesh for strength.
Float-Coat / Finish-Coat — Achieve chosen texture; pigment mixed if through-colour.
Curing & Protection — Mist-spray lime renders; shelter silicone systems from rain.
Final Inspection & Warranty
10. Cost & Budget Planning
Lime Putty (three-coat system)
• Typical cost: £75 – £110 per m²
• Re-decoration: Refresh with limewash every 15–20 yearsSand-Cement (two-coat system)
• Typical cost: £40 – £55 per m²
• Re-decoration: Repaint every 7–10 yearsMonocouche (through-colour render)
• Typical cost: £55 – £70 per m²
• Re-decoration: Generally none required for ~20 yearsSilicone Thin-Coat over External Wall Insulation (EWI)
• Typical cost: £85 – £130 per m²
• Re-decoration: Usually not needed for 25 + years
Always add 10–15 % contingency for hidden substrate defects.
11 Choosing a Specialist Contractor
Heritage Credentials: Lime skills, SPAB or IHBC experience.
Manufacturer Accreditation: Approved installers for Weber, K-Rend, Sto, Baumit.
Coastal Track-Record: Proven performance on seafront elevations.
Samples & Mock-Ups: On-site panels confirm colour and texture.
12 Maintenance & After-Care
Annual Wash-Down: Low-pressure clean to remove salt deposits.
Hairline Monitoring: Fill lime cracks with matching putty; flexi-mastic for silicone.
Re-Limewashing: Every 5-7 years on lime stucco for colour vibrancy.
Silicone Re-Coat: Spray apply tinted top-coat at year 15-20 if colour fade occurs.
13 Frequently Asked Questions
Is monocouche suitable for bungaroosh walls?
No. Bungaroosh needs breathable lime render; monocouche may trap moisture.
Can I mix lime and cement layers?
Avoid—differing flex and breathability often lead to shear cracks.
Will thin-coat silicone stop penetrating damp?
It sheds rain but underlying moisture issues must be fixed first.
14 Further Reading & Spin-Off Articles
Rendering Bungaroosh Walls — Specialist Techniques & Pitfalls
Rendering in Conservation Areas — Dos & Don’ts for Brighton Homeowners
15 Next Step
Book a Render Survey — Moisture readings and substrate analysis.
Safe-Bricks Limited © 2025. All rights reserved.